|
Satesa's single drum laminator/embosser is capable of performing
film to film (including metalized) fabric to fabric and film to
fabric as well as simultaneous embossing.
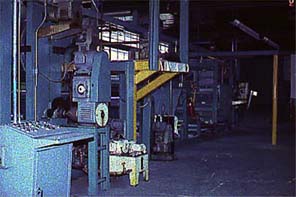
The main head consists of a heat drum, embosser and cooling unit.
The adhesive coated film is delivered for combining to a 36"
diameter hot rolled steel drum which has a 64" chromed face.
The combined mass is brought up to temperature by passing over
three teflon coated boost cans and stripped for embossing prior
to cooling. The aforementioned off-line technique permits
maximum scheduling flexibility. Moreover, printing and top
coating can be intergrated with this system to produce
pleasing decorative effects.
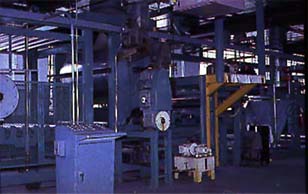
The embossing section has a self-contained hydraulic system
which ensures even travel and application of pressure across
the face of the embossing roll. The hydraulic cylinders have
sufficient stroke to clear the embossing roll for easy removal.
Precision turn screws allow the operator to adjust the running
stroke, too. The entire embossing section is mounted on heavy
duty slides to facilitate embossing (backup) roll changes and
maintenance.
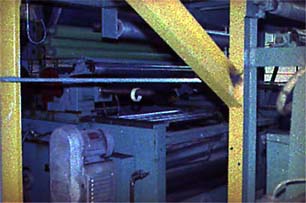
The cooling section consists of two nominal 24" diameter
chromeplated cooling drums. Each drum is jacketed for maximum
cooling efficiency.
The balance of the system consists of an adhesive coater,
dual staggered unwinds (one with J box), slitter, two accumu-
lators and winder.
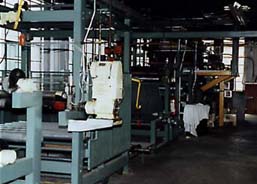
The dual staggered unwinds allow the positioning of two rolls
on its frame, on for running and one for ready-to-splice. Each
unwind spindle has a manual tension brake with automotvie type
lining to ensure smooth tensioning. Side lay adjusters are
provided at each unwind station to allow side positioning of
each roll. The unwind spindle is 1.25" square and one bar is
supplied for each station. Light weight ribbed aluminum cones
lock firmly on the spindle to secure 3" paper cores. In addition,
the fabric unwind has the possibility of feeding a J box to
further compensatory adjustments.
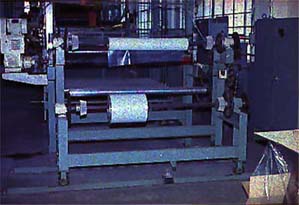

Two accumulators, one for film unwinding and one for product
take-up, permit 40 yard capacity each for continuous operation
during roll changes. The moving carriage has a bottom member
with seven idlers and a top stationary section with eight
idlers. All idlers have free bearings to minimize drag on
the web. Tension in the unit can be altered by adjusting
the state of balance with weights. The moving carriage rides
on hardened and ground steel shafts with ball bearing
followers.
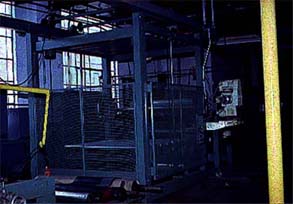
The adhesive coater applies a coating of adhesive to the
traveling web by means of a rotogravure process using an
engraved roll for the applicator (supplied 80 line appli-
cator).
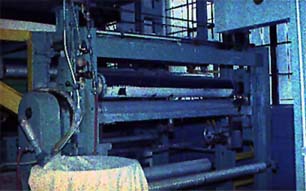
The slitter has a hardened, sleeve type, slitter bar which
allows removal of damaged or worn sleeves. The slitter also
has air actuated circular slitter knives which can be adjusted
by precision screws while running.
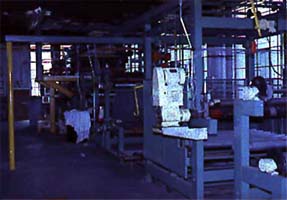
The winder is a dual type, constant tension unit with a
timed-in core speed centerwinder. Quick transfer of cores
is accomplished through tow core positions. The timed-in
speed permits smooth starts and constant speed and tension
through-out build up. This eliminates necking and drawing
of material during starts, providing smooth uniform rolls.
Core holders are supplied for winding 3" paper cores.
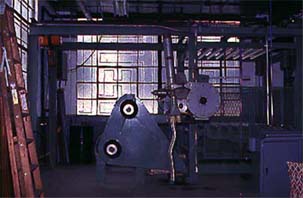
The drive system is through a variable frequency alternator.
All the line drives are variable speed units and can be
adjusted independently, enabling the line operator to correct
and compensate for tension on different substrates. The
system allows for the triming of individual stations while
permitting synchronomous speeding and slowing of the entire
line.
The above line comes with a Dunham-Bush, 20 ton chiller which
feeds the cooling cans and a Malsbary steam generator which
supplies the heat drum and boost cans in exceptionally short
time with steam. An air compressor and full support electrical
panels and control station complete the offering. Any and all
mixers and parts will be shipped, too.
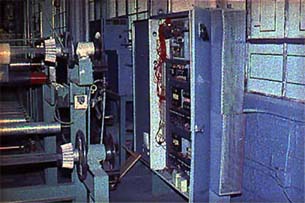
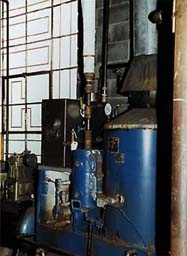
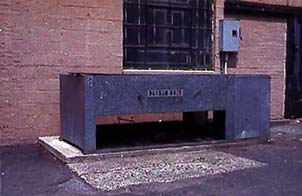
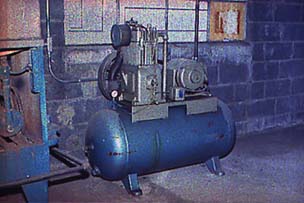
Click Here for technical information
|
|